The GE9X engine dominates modern aviation with its remarkable 134,300 pounds of thrust, powering the Boeing 777X through the skies with 10% greater fuel efficiency than its predecessor. This engineering achievement sets new benchmarks in commercial aviation technology, pushing the boundaries of what aircraft engines can achieve.
Military aviation presents equally impressive feats of engineering. The F135 engine drives the F-35 fighter jet’s exceptional performance, while China’s WS-15 technology emerges as a formidable competitor in the global arena. These powerhouse engines define the capabilities of modern aircraft, enabling commercial carriers to connect distant cities and military forces to maintain air superiority.
This detailed analysis examines five aircraft engines that command the skies in 2025. From thrust capabilities and technical innovations to real-world applications, discover the engineering marvels that power both civilian airliners and military fighters.
Also Read | 10 Most Expensive Fighter Jets
GE9X: The World’s Most Powerful Commercial Aircraft Engine
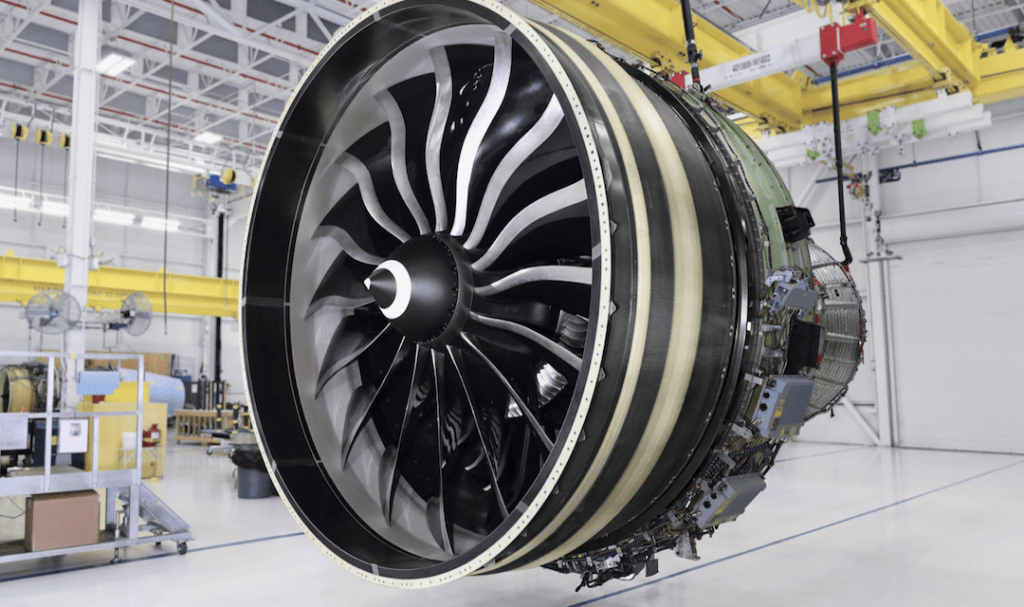
The GE9X engine stands as a testament to modern aviation engineering excellence. GE Aerospace’s flagship powerplant features an impressive 11-foot diameter fan, matching the width of a Boeing 737’s fuselage. This remarkable achievement showcases the rapid advancement of commercial aviation technology.
Technical Prowess of the GE9X
The sheer scale of the GE9X commands attention in the aviation world. The engine stretches 220 inches in length, with a 121-inch diameter and weighs 22,000 pounds. At its heart, 16 fourth-generation carbon fiber composite fan blades work in perfect harmony within a composite housing.
Key Performance Metrics:
Parameter | Specification |
---|---|
Bypass Ratio | 10:1 |
Pressure Ratio | 60:1 |
Core Speed | 11,119 RPM |
The engine’s sophisticated design relies heavily on ceramic matrix composites (CMC). These advanced materials feature in five critical components, including combustor liners and turbine nozzles. Operating at temperatures above 2,400°F, CMC materials deliver twice the strength while weighing just one-third of traditional metal alloys.
Boeing 777X Integration
The GE9X serves exclusively as the powerplant for Boeing’s 777X aircraft family. The engine’s journey to certification demanded rigorous testing, culminating in FAA approval in September 2020 after accumulating nearly 5,000 flight hours and 8,000 flight cycles.
Major airlines have demonstrated strong confidence in the GE9X platform:
- Emirates: 460 engine orders (November 2023)
- Singapore Airlines: 22 orders (Previous year)
Performance Milestones
The GE9X delivers remarkable efficiency gains compared to its predecessors. Fuel consumption shows a 10% reduction versus the GE90-115B, translating to annual fuel savings of 3,000 metric tons – equivalent to removing 2,060 vehicles from roads.
Environmental achievements include:
- 50% reduction in nitrogen oxide emissions compared to peer engines
- NOx emissions 55% below regulatory requirements through Twin Annular Premixing Swirler (TAPS) technology
The engine’s development journey included comprehensive testing against ice, dust, and debris. The successful maiden flight aboard GE’s Flying Test Bed in March 2018 marked a pivotal moment in aviation history.
Also Read | 10 Best Fighter Jets in the World
F135: Dominating Military Aircraft Propulsion
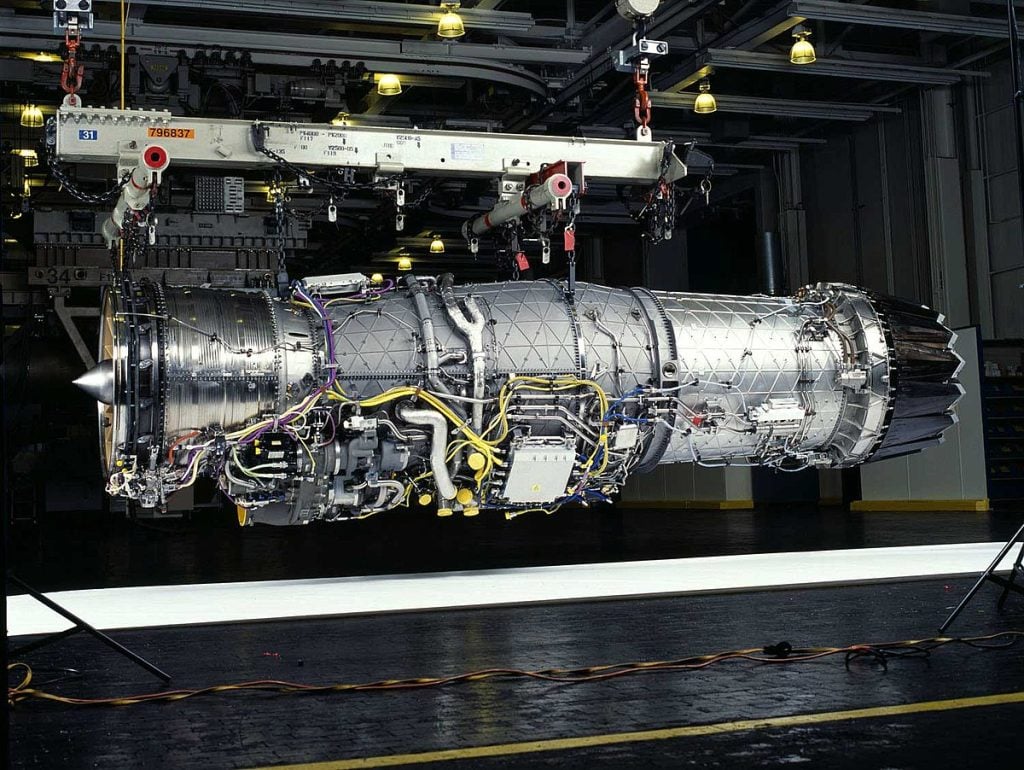
The F135 propulsion system stands as the pinnacle of military aviation engineering. Built upon the battle-proven F119 platform, this remarkable afterburning turbofan powers the F-35 Lightning II through more than 17,500 test hours of demonstrated excellence.
Engineering Excellence
The F135’s sophisticated architecture merges combat reliability with cutting-edge innovation. At its core, the engine combines:
- Three-stage fan system
- Six-stage high-pressure compressor
- Advanced annular combustor
- Dual-stage turbine configuration
Stealth capabilities define the F135’s modern warfare advantage. Traditional spray bars and flameholders give way to thick curved vanes coated with ceramic radar-absorbent materials, ensuring minimal detection signatures.
Maintenance efficiency reaches new heights through the engine’s revolutionary health management system. Ground crews can service all line-replaceable components using just six common hand tools. Real-time diagnostics slash troubleshooting and replacement times by 94% compared to legacy systems.
F-35 Integration Mastery
The F135 demonstrates remarkable versatility across F-35 variants:
Variant | Application | Key Features |
---|---|---|
F135-PW-100/400 | F-35A/C | Conventional/Naval operations |
F135-PW-600 | F-35B | STOVL capability |
The STOVL variant showcases engineering ingenuity through its thrust distribution:
- 46% from two-stage lift fan
- 46% from vectoring exhaust nozzle
- 8% from wing-mounted nozzles
Most impressively, vertical lift operations achieve 50% thrust augmentation without additional fuel consumption.
Performance Supremacy
Raw power defines the F135’s capabilities:
- Military thrust: 28,000 lbf
- Afterburner thrust: 43,000 lbf
The engine enables the F-35 to maintain Mach 1.2 for 150 miles using standard military power. Operational excellence shines through 971,000 flight hours since its 2006 debut, with maintenance intervals extending beyond seven years or 1,200 missions.
Pratt & Whitney’s Engine Core Upgrade (ECU) program promises even greater capabilities. The initiative targets enhanced thrust generation, fuel efficiency improvements, and superior thermal management. Following successful preliminary design review in 2024, the program advances toward securing the F-35’s continued air dominance.
Rolls-Royce Trent XWB: Powering Long-haul Aviation
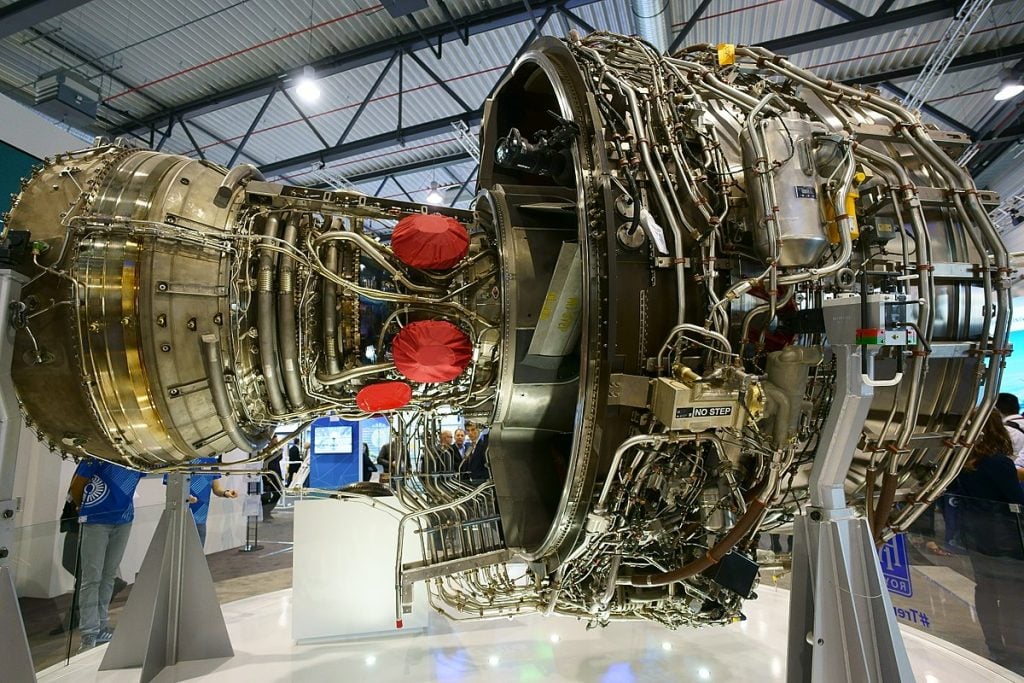
The Rolls-Royce Trent XWB reigns supreme as the world’s most efficient large aero-engine. This engineering masterpiece has amassed an impressive 20 million engine flying hours since its perfect service entry in 2015, demonstrating unmatched reliability in commercial aviation.
Engineering Marvel
The Trent XWB exemplifies Rolls-Royce’s engineering prowess through its signature three-shaft architecture. The engine’s massive 3-meter diameter fan dwarfs the legendary Concorde’s fuselage width. High-precision engineering enables the turbine blades to spin at an astounding 12,500 rpm, with blade tips achieving velocities of 1,200 mph.
Variant Specifications:
Engine Model | Thrust Output | Aircraft Application |
---|---|---|
Trent XWB-84 | 84,200 pounds | A350-900 |
Trent XWB-97 | 97,000 pounds | A350-1000, A350F |
Advanced Technology Features:
- Revolutionary blisk technology reducing weight by 15-18%
- Sophisticated dual-channel FADEC system
- Multi-layer cooling architecture combining internal, impingement, and film methods
Operational Excellence
The Trent XWB demonstrates remarkable versatility across the A350 platform. From quick 45-minute regional flights to marathon 16-hour intercontinental journeys, the engine powers 700 routes connecting 127 cities worldwide.
Performance metrics showcase exceptional reliability:
- 99.9% dispatch reliability rate
- Durability equivalent to 500 global circumnavigations between overhauls
Environmental Leadership
The Trent XWB-powered A350 sets new standards in environmental performance:
- 25% reduction in fuel burn and CO2 emissions versus previous generation
- 15% better fuel efficiency than original Trent series
- Annual fuel cost savings reaching INR 540.03 million per aircraft
Rolls-Royce’s £1 billion upgrade program promises:
- Additional 1% improvement in XWB-84 efficiency
- Enhanced operational durability
- Double time-on-wing for XWB-97 in challenging environments
Sustainable aviation fuel compatibility further strengthens environmental credentials. SAF testing reveals reduced particulate emissions across all operating conditions, while higher energy density offers improved efficiency through reduced fuel mass.
Market success reflects these capabilities, with over 2,600 engines ordered globally, establishing the Trent XWB as the fastest-selling widebody engine. The engine’s ability to connect virtually any two cities worldwide cements its position as the backbone of modern long-haul aviation.
AL-41F: Russia’s Most Powerful Military Engine
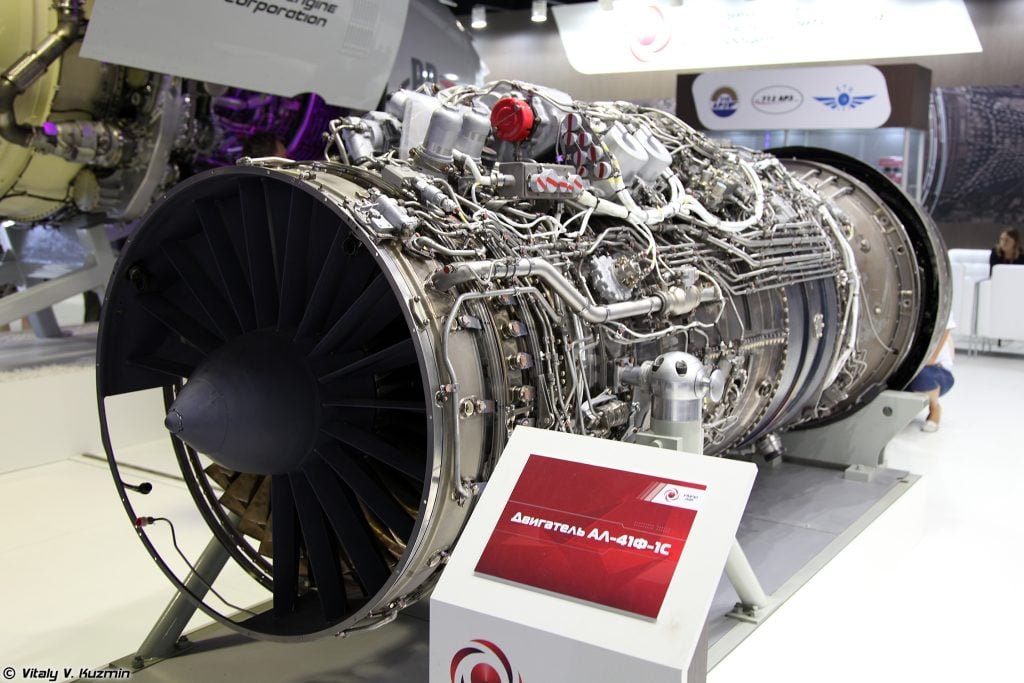
The AL-41F engine series represents Russian military aviation’s technological prowess. This sophisticated powerplant combines advanced thrust vectoring capabilities with modular design principles, marking a significant advancement from its predecessor, the AL-31F.
Technical Mastery
The AL-41F showcases Russian engineering excellence through its modular two-shaft turbofan architecture. Advanced thrust vector control systems and digital management technology define this remarkable engine.
Performance Specifications:
Parameter | Value |
---|---|
Maximum Thrust (with afterburner) | 14,500 kgf |
Military Thrust | 8,800 kgf |
Specific Fuel Consumption | 0.77 kg/kgf·h |
Turbine Inlet Temperature | 1,745°K |
The engine maintains geometric compatibility with AL-31F and AL-31FP platforms. Performance gains stem from revolutionary low-pressure compressor design and advanced turbine cooling systems.
Combat Aircraft Integration
The AL-41F powers Russia’s premier fighter aircraft through specialized variants:
Variant | Aircraft Platform | Role |
---|---|---|
AL-41F-1 (izdeliye 117) | Su-57 | Stealth Fighter |
AL-41F-1S (izdeliye 117S) | Su-35 | Air Superiority |
The engine’s design enables seamless integration into Su-27/Su-30 airframes with minimal modification requirements. Three-dimensional thrust vectoring technology through axisymmetric nozzles delivers superior maneuverability in combat scenarios.
Combat Performance
The AL-41F-1S delivers 18% more thrust than previous engines, generating 144kN compared to 122kN. This power advantage translates directly into combat superiority through enhanced acceleration and maneuverability.
Operational Parameters:
- Maximum rotor speed: 11,500 rpm
- Service ceiling: 20,000 meters
- Cruise fuel consumption: 0.67 kg/kg/h
- Afterburner consumption: 1.92 kg/kg/h
Advanced engineering yields 13% better fuel efficiency while maintaining thrust performance, enabling extended combat radius and increased mission endurance.
Stealth characteristics benefit from advanced materials and aerodynamic refinements, reducing both infrared and radar signatures. These features position the AL-41F as a formidable rival to Western engine designs.
Saturn’s development roadmap includes the AL-51F-1 (izdeliye 30) variant, slated to power future Su-57 aircraft. This progression demonstrates Russia’s commitment to advancing military propulsion technology.
WS-15: China’s Next-Generation Engine Giant
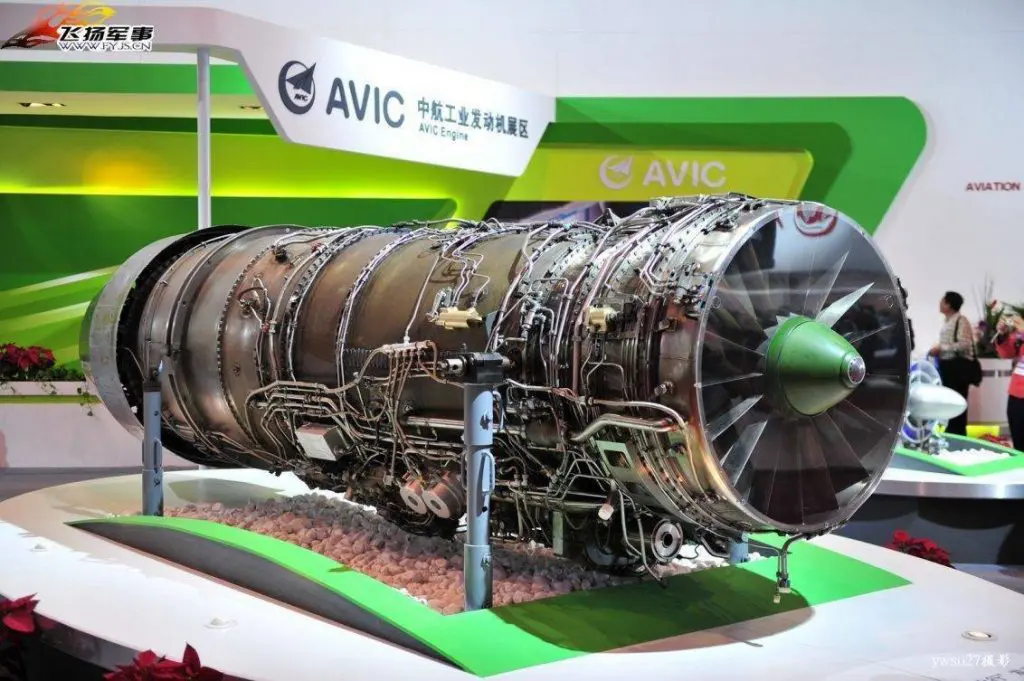
The WS-15 turbofan engine represents China’s emergence as a major player in military aviation technology. From its initial conception in 2006, this sophisticated powerplant demonstrates China’s mastery of advanced propulsion systems, powering the nation’s premier stealth fighter with domestically developed technology.
Engineering Journey
The WS-15, known as “Emei,” faced significant challenges during its development, particularly in thermal management and material durability. The engine’s impressive specifications showcase China’s technological advancement:
Technical Parameters | Specifications |
---|---|
Thrust-to-Weight Ratio | 10 to 11 |
Maximum Diameter | 1.02m |
Total Length | 5.05m |
Mass | 1,862.3kg |
AECC’s breakthrough in metallurgy and production techniques proved crucial for manufacturing super-high temperature components. The development team mastered critical technologies including single-crystal turbine blades, superalloy disks, and specialized fasteners.
J-20B Integration Success
The WS-15’s integration into the J-20B fighter marks a turning point in Chinese military aviation. Single-engine testing commenced in March 2022, progressing to successful dual-engine configurations.
J-20B modifications accommodate the WS-15’s advanced capabilities:
- Enhanced DSI inlet design for optimal airflow
- Streamlined fuselage contours
- Advanced nosecone profile with deeper spine
- Optimized cockpit positioning
Current operational data reveals impressive performance, with turbine inlet temperatures reaching 1,477 degrees Celsius. Flight testing demonstrates reduced takeoff distances and significantly quieter operation compared to previous powerplants.
Performance Benchmarks
The WS-15 stands among global leaders in thrust generation:
- Maximum thrust: 36,000 pounds (afterburner)
- Development target: 40,000 pounds
Operating Parameters:
- Base thrust output: 10 tons
- Afterburner fuel consumption: 2.02kg/daN/h
- Standard fuel consumption: 0.665kg/daN/h
- Air mass flow: 138kg/s
Engine architecture delivers a bypass ratio of 0.382 and pressure ratio of 28.71, enabling the J-20B’s supercruise capability – sustained supersonic flight without afterburner engagement. Advanced systems provide enhanced electrical generation and thermal management.
Future development paths include thrust vectoring technology, though not implemented in initial production units. The engine’s modular design supports potential adaptation for China’s sixth-generation fighter program.
Current efforts focus on reliability improvements and maintenance optimization, targeting standards set by mature WS-10 variants. The announcement of WS-15 mass production by Zhang Yong at AECC’s Beijing Institute signals China’s arrival as a major force in military engine technology.
World’s Most Powerful Aircraft Engines: Performance Comparison
The competition for aviation supremacy unfolds through five remarkable engines, each pushing the boundaries of aerospace engineering. From commercial giants to military marvels, these powerplants demonstrate the pinnacle of human innovation in aircraft propulsion.
Performance Overview
Engine Capabilities:
Engine | Maximum Thrust | Aircraft Platform | Current Status |
---|---|---|---|
GE9X | 134,300 lbs | Boeing 777X | FAA certified (2020) |
F135 | 43,000 lbf | F-35 Lightning II | Operational with upgrades |
Trent XWB | 84,200-97,000 lbs | Airbus A350 | 20M+ flight hours |
AL-41F | 31,967 lbs | Su-57, Su-35 | Operational |
WS-15 | 36,000-40,000 lbs | J-20B | Production phase |
Technical Excellence
Each engine brings unique innovations to modern aviation:
Commercial Leaders:
- GE9X: Revolutionary ceramic matrix composites enable 10% better fuel efficiency
- Trent XWB: Three-shaft architecture delivers 99.9% dispatch reliability
Military Powerhouses:
- F135: Stealth augmentor technology maintains Mach 1.2 for 150 miles
- AL-41F: Three-dimensional thrust vectoring provides superior maneuverability
- WS-15: Advanced thermal management supports supercruise capability
Environmental Impact
Efficiency improvements showcase environmental consciousness:
- GE9X: 55% below NOx emission requirements
- Trent XWB: 25% reduction in fuel burn versus previous generation
- AL-41F: 13% better fuel efficiency while maintaining performance
The Future of Aircraft Propulsion
Modern aircraft engines stand as testaments to human ingenuity and engineering excellence. The GE9X commands respect with its unprecedented 134,300 pounds of thrust, while the F135 demonstrates military superiority through advanced stealth technology and combat-proven reliability.
Each powerplant brings unique strengths to aviation’s future:
Commercial Excellence:
- GE9X: Setting new standards in thrust generation
- Trent XWB: Achieving 99.9% dispatch reliability
- Both engines leading environmental consciousness
Military Innovation:
- F135: Mastering stealth propulsion
- AL-41F: Perfecting thrust vectoring technology
- WS-15: Challenging established Western designs
The race for propulsion supremacy drives continuous advancement. Engine manufacturers push beyond conventional limits through:
- Revolutionary material science
- Advanced thermal management
- Sophisticated digital control systems
- Enhanced environmental performance
These remarkable machines will continue shaping aviation’s future, connecting cities and defending nations with ever-increasing capability and efficiency.